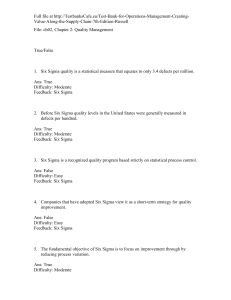
FREE Sample Here
... Employees are most directly involved in kaizen when they are determining solutions to their own problems. Employees are the real experts in their immediate workspace. In its most basic form kaizen is a system in which employees identify many small improvements on a continual basis and implement thes ...
... Employees are most directly involved in kaizen when they are determining solutions to their own problems. Employees are the real experts in their immediate workspace. In its most basic form kaizen is a system in which employees identify many small improvements on a continual basis and implement thes ...
Six Sigma takes a handful of proven methods and trains a small
... People create results. Involving all employees is essential to GE's quality approach. GE is committed to providing opportunities and incentives for employees to focus their talents and energies on satisfying customers. All GE employees are trained in the strategy, statistical tools and techniques of ...
... People create results. Involving all employees is essential to GE's quality approach. GE is committed to providing opportunities and incentives for employees to focus their talents and energies on satisfying customers. All GE employees are trained in the strategy, statistical tools and techniques of ...
How Business Process Improvement Methodologies Can Improve
... organizational culture. Every methodology seeks to improve the business and ultimately increase its profits and this is most successfully achieved by eliminating existing waste and improving overall quality. Additionally, workers at every level play an integral role in the success of implementing an ...
... organizational culture. Every methodology seeks to improve the business and ultimately increase its profits and this is most successfully achieved by eliminating existing waste and improving overall quality. Additionally, workers at every level play an integral role in the success of implementing an ...
True Confessions of a Lean Six Sigma Black Belt
... • Separated by functional roles (swim lanes) • Can be eye-opening for staff to see what employees in other departments/units do as part of a process • Helps identify where waste occurs (TimUWood) ...
... • Separated by functional roles (swim lanes) • Can be eye-opening for staff to see what employees in other departments/units do as part of a process • Helps identify where waste occurs (TimUWood) ...
Six Sigma - the Latest Approach in the Ongoing Development of
... produces an output that adds value to the organization • All work is performed in (interconnected) processes – Easy to see in some situations (manufacturing) – Harder in others ...
... produces an output that adds value to the organization • All work is performed in (interconnected) processes – Easy to see in some situations (manufacturing) – Harder in others ...
Six Sigma
Six Sigma is a set of techniques and tools for process improvement. It was introduced by engineer Bill Smith while working at Motorola in 1986. Jack Welch made it central to his business strategy at General Electric in 1995. Today, it is used in many industrial sectors.Six Sigma seeks to improve the quality of the output of a process by identifying and removing the causes of defects (errors) and minimizing variability in manufacturing and business processes. It uses a set of quality management methods, mainly empirical, statistical methods, and creates a special infrastructure of people within the organization, who are experts in these methods. Each Six Sigma project carried out within an organization follows a defined sequence of steps and has specific value targets, for example: reduce process cycle time, reduce pollution, reduce costs, increase customer satisfaction, and increase profits.The term Six Sigma originated from terminology associated with manufacturing, specifically terms associated with statistical modeling of manufacturing processes. The maturity of a manufacturing process can be described by a sigma rating indicating its yield or the percentage of defect-free products it creates. A six sigma process is one in which 99.99966% of all opportunities to produce some feature of a part are statistically expected to be free of defects (3.4 defective features / million opportunities), although, as discussed below, this defect level corresponds to only a 4.5 sigma level. Motorola set a goal of ""six sigma"" for all of its manufacturing operations, and this goal became a by-word for the management and engineering practices used to achieve it.